Understanding Die Casting Die: A Comprehensive Guide
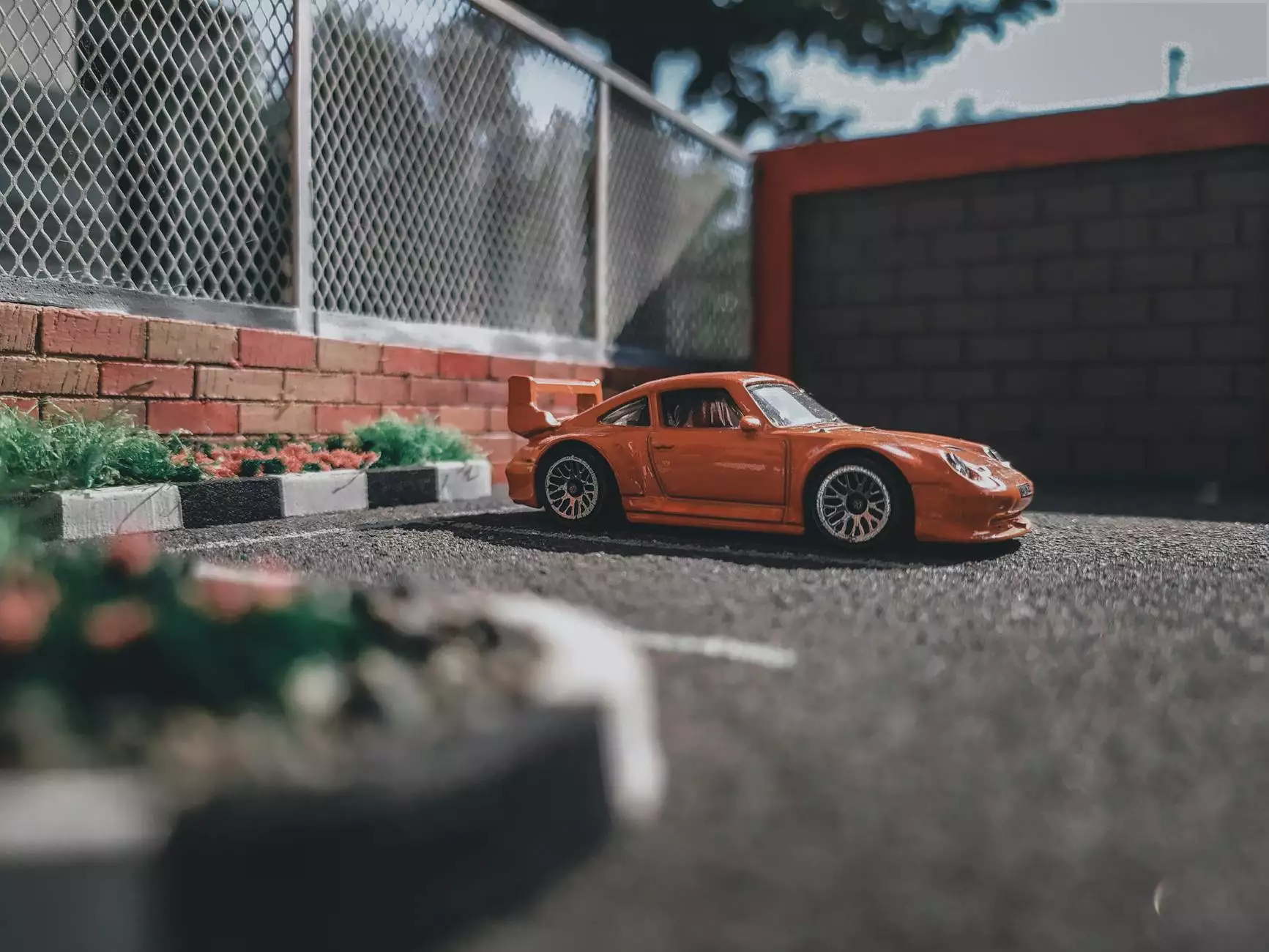
The world of metal fabrication is complex, and one of the key elements driving this industry is the die casting die. In this article, we will delve into everything you need to know about die casting dies, their importance, and the benefits they offer in various applications. This information aims to position your understanding of this subject well, whether you are a manufacturer, engineer, or enthusiast.
What is a Die Casting Die?
A die casting die is a specialized mold used in the die casting process, which involves forcing molten metal into a mold cavity under high pressure. Unlike traditional casting, die casting allows for the production of intricate shapes and designs with high dimensional accuracy and repeatability. The die itself is typically made from high-strength steel or alloy to withstand the extreme pressures and temperatures involved in the process.
Key Components of Die Casting Die
- Die Cavity: The internal shape into which molten metal is injected.
- Core: Inserts that define internal geometries and features.
- Cooling Channels: Systems that manage the temperature to ensure even cooling, enhancing the quality of the cast.
- Sprue: The channel through which molten metal enters the die cavity.
- Runner System: A network that directs the molten metal to different cavities in multi-cavity dies.
The Die Casting Process
The die casting process can be broken down into several stages, each critical to ensuring high-quality output. The main steps are:
- Preparation: The die is prepped with a release agent to facilitate the easy removal of the finished part.
- Injection: Molten metal is injected into the die at high speed and pressure.
- Cooling: The molten metal cools and solidifies, taking the shape of the die.
- Ejection: Once the part has cooled sufficiently, ejectors are used to remove the cast from the die.
- Trimming: Excess material is removed, and the part is finished according to specifications.
Advantages of Die Casting
The die casting process and the use of die casting die bring several advantages to manufacturers and industries. Some of these include:
- High Precision: Die casting allows for tighter tolerances compared to other manufacturing processes.
- Cost-Effective for Large Runs: The initial investment in dies can be high, but the cost per unit decreases significantly with large production runs.
- Complex Geometries: The flexibility of die design permits complex shapes that are difficult to achieve with other techniques.
- Surface Finish: Parts produced by die casting typically have a good surface finish, reducing the need for further machining.
- Material Versatility: A wide range of metals can be used in die casting, including aluminum, zinc, and magnesium.
Applications of Die Casting
Die casting is widely used across various industries due to its versatility and efficiency. Some notable applications include:
- Automotive Components: From engine blocks to transmission cases, die casting plays a crucial role in the automotive industry.
- Consumer Electronics: Housings for electronic devices are often produced using die casting for their lightweight and durable properties.
- Aerospace Parts: High-strength components required for aviation are often manufactured through die casting.
- Household Items: Many small appliances and tools utilize die-cast parts for their functionality and design.
Choosing the Right Die Casting Die Manufacturer
Selecting a reliable and proficient manufacturer for your die casting die is crucial for the success of your production process. Consider the following factors:
- Experience: Look for manufacturers with a proven track record in the die casting industry.
- Technological Capability: Advanced equipment and technology can significantly enhance the quality of the final product.
- Customization: The ability to design custom dies according to specific project requirements is a must.
- Quality Control: Ensure the manufacturer has strict quality assurance measures in place to maintain high standards.
- Customer Support: Good communication and support are essential for troubleshooting and project adjustments.
DeepMould's Expertise in Die Casting Die
At DeepMould, we pride ourselves on being leaders in the metal fabrication sector. Our expertise in die casting die is unmatched, and we have established ourselves as a trusted partner for industries globally. Here’s what sets us apart:
- State-of-the-Art Facilities: Our manufacturing plants are equipped with the latest technology to ensure precision and efficiency.
- Custom Solutions: We tailor our die casting dies to meet the unique needs of our clients, ensuring optimal performance.
- Expert Team: Our team comprises skilled engineers and designers with years of experience in die casting.
- Commitment to Quality: We adhere to the highest standards of quality control, ensuring every product meets specifications.
- Sustainability Practices: DeepMould is dedicated to environmentally friendly practices throughout our manufacturing processes.
Future Trends in Die Casting
As the demand for metal products continues to grow, the die casting industry is evolving rapidly. Key trends to watch include:
- Increased Automation: Automation in the die casting process is set to enhance efficiency and reduce production costs.
- 3D Printing Technologies: Integration of 3D printing into die manufacturing is revolutionizing design possibilities and prototyping.
- Advanced Materials: Research into new alloys and materials is expanding the capabilities of die casting.
- Sustainability Efforts: A focus on sustainable practices in metalworking is becoming increasingly important to consumers and businesses alike.
- Smart Manufacturing: IoT and data analytics are being utilized to optimize die casting processes through real-time monitoring.
Conclusion
In conclusion, the die casting die remains a fundamental aspect of the metal fabrication industry, enabling manufacturers to produce high-quality, precise, and complex parts efficiently. Whether your focus is automotive, aerospace, or consumer goods, understanding the significance of die casting can lead to better decision-making in production processes.
For businesses seeking a reliable partner in this realm, DeepMould stands out as a beacon of excellence, providing state-of-the-art solutions tailored to meet the needs of our clients. With ongoing innovations and a commitment to quality, we are excited to shape the future of die casting together.